Preamble
For your convenience I have listed below posts in this series:
Arte Latino Textiles
Arte Latino Prints
Arte Latino Sculptures - Part I
Arte Latino Sculptures - Part II
Arte Latino Paintings - Part I
Arte Latino Paintings - Part II
Arte Latino Prints
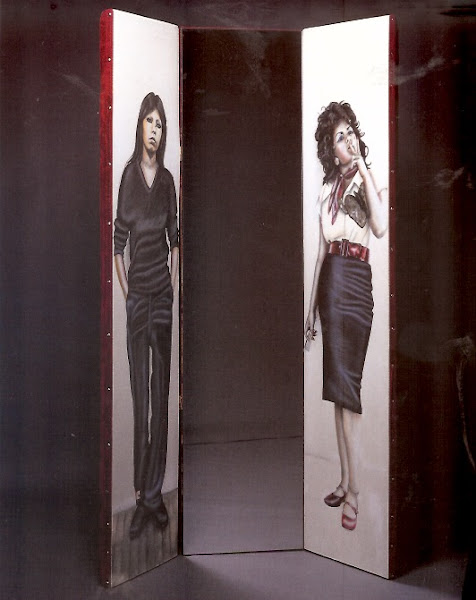
Artist and Title of Work: Judith Baca, Las Tres Marias (The Three Marys) (1976).
Technique and Materials: Colored pencil on paper, wood, cloth and mirror.
Size: 173.4 x 127.6 x 5.7 cm.
Courtesy: Smithsonian American Art Museum.
Acquisition: Museum purchase possible by W.T. Evans.
Comment[1]: Two strong women flank a mirror that serves to place the viewer at the center of the visual field. At left is a modern young chola (contemporary member of a street gang), dressed casually and gazing unflinchingly at the viewer, her hands in her pocket. At the right is a portrait of Baca dressed as a pachuca (member of a street gang from the 1940s) taking a drag from her cigarette. Through the updating of the centuries old theme of the three Marys of the crucifixion, Baca explores personal and cultural identity and challenges the viewers to position themselves - literally and figuratively - on such issues as gender, ethnicity and class.
Artist and Title of Work: Maria Castagliola, A Matter of Trust (1994).
Technique and Materials: Paper on fiberglass with cotton thread.
Size: 183 x 183 x 0.3 cm.
Acquisition: Gift of Artist.
Comment[1]: "There are very few relationships," the artist states, "in which you can share everything and trust that there is going to be support and understanding." Castagliola collected these secrets with the understanding that they were never to be opened. To ensure this, she sealed the quilt between sheets of fiberglass window screen. This added a formal element to her artwork, the padded surface shimmering with yet another pattern.
Artist and Title of Work: Maria Martinez-Canas, Totem Negro XVI (1992).
Technique and Materials: Silver print.
Size: 135.9 x 23.8 cm.
Courtesy: Smithsonian American Art Museum.
Acquisition: Smithsonian Institution Collections Acquistion Program.
Comment[1]: In Totem Negro XVI, carefully collaged signs and symbols give visual form to Martinez-Canas' feelings about being an exile. These fragments of ancient manuscripts, postage stamps, geographic forms, pre-Columbian temples, and maps reflect her struggle to reclaim her Cuban heritage. The collaged geographic and organic shapes are scratched and drawn upon, before being adhered to sheets of clear plastic that serve as handmade 'negatives'. Martinez-Canas then prints a limited edition of contact prnts on black-and-white photographic paper.
Artist and Title of Work: Delilah Montoya, Los Jovenes (Youth) (1993).
Technique and Materials: Collotype.
Size: 20.3 x 25.4 cm.
Courtesy: Smithsonian American Art Museum.
Acquisition: Donation by Horace W. Goldsmith Foundation.
Comment[1]: Montoya uses a 19th century collotype technique in which the negative is inked and printed, a process that blends photographic documentation and manipulation. Los Jovenes is a part of a series entitled El Corazon Sagrado (The Sacred Heart), a religious and cultural symbol that blends European Catholicism and Aztec philosophy. According to Chicano art scholar Dr Tomas Ybarra-Frausto, 'the heart has served as a symbol of resilience, bound both to visual iconography and to the process of creation itself' In this heartfelt work, Montoya has created a striking image of family strength - and love.
Artist and Title of Work: Vik Muniz, Sugar Children series (1996).
Technique and Materials: Silver prints.
Size: 35.6 x 27.9 cm.
Courtesy: Smithsonian American Art Museum.
Acquisition: Museum purchase made possible by the Horace W. Goldsmith Foundation.
Comment[1]: The power of the image lies in its ability to be underestimated. They're sweet simple things. You think you know what you're looking at," says Muniz, who wants the viewer to look anew at these representations. These prints asks the eye to question what it sees, posing a relationship between reality, truth, representation and memory.
Artist and Title of Work: Kathy Vargas, Missing #3 (1992).
Technique and Materials: Silver prints.
Size: Each 61 x 50.8 cm.
Courtesy: Smithsonian American Art Museum.
Acquisition: Museum purchase made possible by the Horace W. Goldsmith Foundation.
Comment[1]: Missing #3 consists of six hand-colored gelatin silver prints that the artist created through multiple-exposure photography. Together they create a haunting, poetic memento mori (reminder of cycle of life, death and resurrection). In this X-ray like image, a dark and lifeless bird is tucked into a band of clothing, feathers are strewn about, and broken twigs form an abstract pattern. The inspiration for the artwork came from a dream in which Vargas was lying in a coffin. As mourners paid their final respects, she was transformed into a bird. This is symbolized in the central panels, in which the bird and the skeleton merge. To the right, she said, 'is an image...waiting to wing out, but unwilling to walk for now.' Multiple hands appear, the palm in the upper left print mirrored by the skeletal one in the lower center. The hand colored image bears the artist's imprint throughout. An inscription on the back reads: 'At some point the two dreams merge into a recognizable self-portrait.'
Reference:
[1] J. Yorba, Arte Latino: Treasures from the Smithsonian American Art Museum, Watson-Guptill Publications, New York (2001).
Preamble
For your convenience I have listed below other posts on tapestries:
The Australian Tapestry Workshop
The Australian Tapestry Workshop (1976 – 1985)
The Australian Tapestry Workshop (1986 – 1995)
The Australian Tapestry Workshop (1996 - 2004)
Tapestry Creations of the 1980s
Tapestries from the USA
Modern Australian Tapestries
Tapestries from the USA
America has a rich history in producing tapestries. Below are a few selections from American tapestry artists.
Creator and Title of Tapestry: Archie Brennan, Drawing Series XLIV:Study.
Materials and Techniques: Tapestry; cotton warp, raw silk, wool, and cotton weft.
Size: 22.25 x 11.25 inches.
Creator and Title of Tapestry: Aase Vaslow, This is Not the Real Me.
Materials and Techniques: Beaded tapestry; loom woven mounted; linen, seed beads.
Size: 7 x 5 inches.
Photo Courtesy: Mignon Naegeli.
Creator and Title of Tapestry: Priscilla Lynch, Proof of Identity.
Materials and Techniques: Gobelin tapestry; cotton warp, wool weft.
Size: 25 x 25 inches.
Comment[1]: After my wallet and all of my identification were stolen, I started thinking of how we prove our identity - photo, fingerprint, numbers, DNA profile - none of which tell anyone who we really are.
Creator and Title of Tapestry: Teresa Graham Salt, Middle-Age Panic.
Materials and Techniques: Tapestry; silk buttonhole-twist thread.
Size: 8 x 6 inches.
Creator and Title of Tapestry: Kathy Spoering, Croquet Coquette.
Materials and Techniques: Tapestry; wool weft on cotton warp.
Size: 53 x 36 inches.
Creator and Title of Tapestry: Janita Loder, You're in the Army Now!
Materials and Techniques: Tapestry, painted, hand dyed; wool weft, cotton warp, fabric paint and dye.
Size: 15 x 15 inches.
Comment[1]: The inspiration for this piece was a family photo and memories of my children when they were young.
Creator and Title of Tapestry: Tori S. Kleinert, Terroristic Semblance: Destruction of the Fold.
Materials and Techniques: Small format tapestry; linen, cotton.
Size: 9 x 10 inches.
Photo Courtesy: J.M. Kleinert.
Creator and Title of Tapestry: Sarah Swett, Escape Literature.
Materials and Techniques: Flat tapestry, two-sided weft-faced plain weave; wool warp, wool weft, natural dyes.
Size: 48 x 36 inches.
Photo Courtesy: Mark laMoreaux.
Creator and Title of Tapestry: Shelley Socolofsky, Well of Surrender.
Materials and Techniques: Gobelin tapestry; wool, silk, cotton.
Size: 84 x 60 inches.
Photo Courtesy: Ken Altman.
Reference:
[1] Fibrearts Design - Book 7, Editor S.M. Kieffer, Larks Books, New York (2004).
Preamble
I started this blogsite on 26 August, 2010. My first blog was ArtCloth:Engaging New Visions. We have just passed over 1,000,435 plus viewers coming to our blogspot. Thank you for your support!
To my followers, and to my occasional visitors, thanks for supporting this blogspot. Who would have thought that when I started my musings, it would be so interesting to so many of you?
My favourite motto whenever I contemplate a new adventure is - Be Brave, The Rest Will Follow! Many of the posts on this blogspot reflect this attitude.
Thanks once again!
Marie-Therese
For your convenience I have listed below other posts in this series:
Diversity of African Textiles
African Textiles: West Africa
Stripweaves (West Africa) - Part I
Stripweaves (West Africa) - Part II
Stripweaves (West Africa) - Part III
Stripweaves (West Africa) - Part IV
Djerma Weaving of Niger and Burkina-Faso
Woolen Stripweaves of the Niger Bend
Nigerian Horizontal - Loom Weaving
Yoruba Lace Weave
Nigerian Women's Vertical Looms
The Supplementary Weft Cloths of Ijebu-Ode and Akwete
African Tie and Dye
Tie and Dye of the Dida, Ivory Coast
African Stitch Resist
Yoruba Stitch Resist
Yoruba: Machine-Stitched Resist Indigo-Dyed Cloth
Yoruba and Baulé Warp Ikat
Nigerian Starch-Resist (by hand)
Stencilled Starch-Resist
Woolen Stripweaves of the Niger Bend[1]
Apart from the area around Cape Verde, the only region in West Africa with climatic conditions suitable for rearing sheep is the Niger Bend. It is cool and has enough pasture (from the flooding of the Niger).
Blanket "Mumuye" from the Fulani people of the Niger Bend region, Mali and Niger.
Woven with white sheep's wool on a horizontal strip loom, they are made up of four to six panels, each approximately 15 cm (6 inches) wide, sewn selvedge to selvedge. Each strip has supplementary weft decoration, with motifs influenced by North Africa. The Fulani name all different motifs. The designs on the upper and lower borders symbolize water and fertility, while the central motif represents the paths taken by the Fulani herds. The strips are sown together so that the 'Moorish' motifs join up to form lateral bands of pattern.
Part of an old arkilla kerka woolen cover woven by the Fulani for the Tuareg.
Itinerant Fulani weavers travel to Tuareg encampments to weave very large chequered tent dividers or bed covers known by such names as arkilla jengo and arkilla kerka. Like khaasa, the warp is made of cotton and the weft of wool. The combined thickness gives not only warmth at night but also protection from the abundant and troublesome mosquitoes. Arkilla are bought by rich Fulani, marabouts (holy men), nomadic Tuareg and Moors.
Arkilla kerka, a very long wool and cotton cover woven and used by the Fulani to divide off the place for the bridal bed from the reception area in their dwellings.
A man selling khaasa Fulani woolen blanket by the river Niger.
Sheep are shorn by Fulbe (noble-caste) Fulani shepards. The wool is spun by women and given to Maabube (lower-caste) Fulani weavers, who weave it into khaasa strips. Sewing together the strips and finishing are tasks carried out by the Fulbe. The same process takes place when the Maabube weave for the Tuareg, though the wool is Tuareg.
Khaasa Fulani woolen blanket, Mopti, Mali. Berber weavers in southern Algeria weave very similar textiles, which may be a model for the khaasa or an export-driven imitation.
According to the acknowledged expert on the subject, Dr Pascal James Imperato, Fulani looms are made up of twelve pieces of wood. Four are driven vertically into the ground. The cotton warps are tied around a stone drag weight on a wooden or metal sledge. From the anchor, the warp passes over a beam and down through two foot-operated string heddles, which are hung from a wooden pully assembly through a reed-beater and end around a cloth beam.
Arkilla munga wedding blanket woven by the Fulani for the Tuareg.
Reference:
[1] J. Gillow, African Textiles, Thames & Hudson Ltd, London (2003).
Preamble
This is the one hundredth and eleventh post in the "Art Resource" series, specifically aimed to construct an appropriate knowledge base in order to develop an artistic voice in ArtCloth.
Other posts in this series are:
Glossary of Cultural and Architectural Terms
Units Used in Dyeing and Printing of Fabrics
Occupational, Health & Safety
A Brief History of Color
The Nature of Color
Psychology of Color
Color Schemes
The Naming of Colors
The Munsell Color Classification System
Methuen Color Index and Classification System
The CIE System
Pantone - A Modern Color Classification System
Optical Properties of Fiber Materials
General Properties of Fiber Polymers and Fibers - Part I
General Properties of Fiber Polymers and Fibers - Part II
General Properties of Fiber Polymers and Fibers - Part III
General Properties of Fiber Polymers and Fibers - Part IV
General Properties of Fiber Polymers and Fibers - Part V
Protein Fibers - Wool
Protein Fibers - Speciality Hair Fibers
Protein Fibers - Silk
Protein Fibers - Wool versus Silk
Timelines of Fabrics, Dyes and Other Stuff
Cellulosic Fibers (Natural) - Cotton
Cellulosic Fibers (Natural) - Linen
Other Natural Cellulosic Fibers
General Overview of Man-Made Fibers
Man-Made Cellulosic Fibers - Viscose
Man-Made Cellulosic Fibers - Esters
Man-Made Synthetic Fibers - Nylon
Man-Made Synthetic Fibers - Polyester
Man-Made Synthetic Fibers - Acrylic and Modacrylic
Man-Made Synthetic Fibers - Olefins
Man-Made Synthetic Fibers - Elastomers
Man-Made Synthetic Fibers - Mineral Fibers
Man Made Fibers - Other Textile Fibers
Fiber Blends
From Fiber to Yarn: Overview - Part I
From Fiber to Yarn: Overview - Part II
Melt-Spun Fibers
Characteristics of Filament Yarn
Yarn Classification
Direct Spun Yarns
Textured Filament Yarns
Fabric Construction - Felt
Fabric Construction - Nonwoven fabrics
A Fashion Data Base
Fabric Construction - Leather
Fabric Construction - Films
Glossary of Colors, Dyes, Inks, Pigments and Resins
Fabric Construction – Foams and Poromeric Material
Knitting
Hosiery
Glossary of Fabrics, Fibers, Finishes, Garments and Yarns
Weaving and the Loom
Similarities and Differences in Woven Fabrics
The Three Basic Weaves - Plain Weave (Part I)
The Three Basic Weaves - Plain Weave (Part II)
The Three Basic Weaves - Twill Weave
The Three Basic Weaves - Satin Weave
Figured Weaves - Leno Weave
Figured Weaves – Piqué Weave
Figured Fabrics
Glossary of Art, Artists, Art Motifs and Art Movements
Crêpe Fabrics
Crêpe Effect Fabrics
Pile Fabrics - General
Woven Pile Fabrics
Chenille Yarn and Tufted Pile Fabrics
Knit-Pile Fabrics
Flocked Pile Fabrics and Other Pile Construction Processes
Glossary of Paper, Photography, Printing, Prints and Publication Terms
Napped Fabrics – Part I
Napped Fabrics – Part II
Double Cloth
Multicomponent Fabrics
Knit-Sew or Stitch Through Fabrics
Finishes - Overview
Finishes - Initial Fabric Cleaning
Mechanical Finishes - Part I
Mechanical Finishes - Part II
Additive Finishes
Chemical Finishes - Bleaching
Glossary of Scientific Terms
Chemical Finishes - Acid Finishes
Finishes: Mercerization
Finishes: Waterproof and Water-Repellent Fabrics
Finishes: Flame-Proofed Fabrics
Finishes to Prevent Attack by Insects and Micro-Organisms
Other Finishes
Shrinkage - Part I
Shrinkage - Part II
Progressive Shrinkage and Methods of Control
Durable Press and Wash-and-Wear Finishes - Part I
Durable Press and Wash-and-Wear Finishes - Part II
Durable Press and Wash-and-Wear Finishes - Part III
Durable Press and Wash-and-Wear Finishes - Part IV
Durable Press and Wash-and-Wear Finishes - Part V
The General Theory of Dyeing – Part I
The General Theory of Dyeing - Part II
Natural Dyes
Natural Dyes - Indigo
Mordant Dyes
Premetallized Dyes
Azoic Dyes
Basic Dyes
Acid Dyes
Disperse Dyes
Direct Dyes
Reactive Dyes
Sulfur Dyes
Blends – Fibers and Direct Dyeing
The General Theory of Printing
There are currently eight data bases on this blogspot, namely, the Glossary of Cultural and Architectural Terms, Timelines of Fabrics, Dyes and Other Stuff, A Fashion Data Base, the Glossary of Colors, Dyes, Inks, Pigments and Resins, the Glossary of Fabrics, Fibers, Finishes, Garments and Yarns, Glossary of Art, Artists, Art Motifs and Art Movements, Glossary of Paper, Photography, Printing, Prints and Publication Terms and the Glossary of Scientific Terms, which has been updated to Version 3.5. All data bases will be updated from time-to-time in the future.
If you find any post on this blog site useful, you can save it or copy and paste it into your own "Word" document etc. for your future reference. For example, Safari allows you to save a post (e.g. click on "File", click on "Print" and release, click on "PDF" and then click on "Save As" and release - and a PDF should appear where you have stored it). Safari also allows you to mail a post to a friend (click on "File", and then point cursor to "Mail Contents On This Page" and release). Either way, this or other posts on this site may be a useful Art Resource for you.
The Art Resource series will be the first post in each calendar month. Remember - these Art Resource posts span information that will be useful for a home hobbyist to that required by a final year University Fine-Art student and so undoubtedly, some parts of any Art Resource post may appear far too technical for your needs (skip over those mind boggling parts) and in other parts, it may be too simplistic with respect to your level of knowledge (ditto the skip). The trade-off between these two extremes will mean that Art Resource posts will hopefully be useful in parts to most, but unfortunately may not be satisfying to all!
Introduction
Sulfur dyes are so called because they contain sulfur (S) atom(s). Sulfur dyes have been used as cotton dyes for over 100 years. The range of sulfur dyes is limited to dull colors from yellow to black. None are very bright and reds are almost absent apart from a few dull maroons and bordeaux shades. The fibers that are most readily colored with sulphur dyes are the natural and man-made cellulosic fibers.
Sulfur Dyes. See - http://www.alibaba.com/product-gs/442451744/sulfur_dyes.html - for further information about these dyes.
Little is known about the chemical structure of sulfur dyes, even though they are thought to contain a thiazine ring.
Portion of a sulfur dye molecule.
Note: The complete structure is still not known. The thiazine ring is the –N=C-S- portion of the above structure, where N, C and S are nitrogen, carbon and sulfur respectively.
Courtesy of reference[1].
Sulfur dyes are water insoluble and so must first be reduced into a soluble form. They are produced by chemically reacting compounds as p-aminophenol and dinitronaphthalene with sulfur. A simplistic scheme for their production is given below.
Production of a sulfur dye.
Note: The old spelling of Sulfur is used in this schematic.
Courtesy reference[1].
Dyeing with Sulfur Dyes
Sulfur dyes are insoluble in water. An aqueous solution of the sulfur dye is effected by reacting some sulfur dyes with sodium sulphide and others with sodium hydrosulfite. The role of sodium sulfide or sodium hydrosulfite is to reduce sulfur to produce the water soluble or leuco form of the dye. In some instances the addition of sodium carbonate may be necessary to achieve the desired alkalinity. In this reduced or leuco form, sulphur dyes are substantive to cellulose fibers. To achieve dye exhaustion, it is necessary to add an electrolyte such as sodium chloride to the dye liquor.
To obtain adequate penetration and a satisfactory rate of dyeing, the dye liquor is heated. This has a two-fold effect:
(i) It enlarges the entry and internal voids of the amorphous regions of the fiber polymer system enabling deeper penetration into the fiber.
(ii) It increases the kinetic energy of all the constituents, thereby increasing the rate of dye uptake by the fiber polymer system.
Once the dye is within the amorphous regions of the fiber polymer system, the reduced sulfur (which is soluble) is converted to its original insoluble form, via an oxidation treatment with a mild reagent such as sodium perborate.
Printing with Sulfur Dyes
Sulfur dyes are generally not used for printing textile materials.
Properties of Sulfur Dyes
Light-Fastness
The light-fastness rating of sulfur dyes is about 4, which translates as fair. After-treatments with metal salts improve the light-fastness rating to 5. The initial fair rating is attributed to the instability of the chromophores of the sulfur dyes with respect to UV sunlight. On the other hand, metal ions improve the stability of the sulfur dye chromophores with respect to UV sunlight, increasing their light-fastness rating.
Wash-Fastness
Sulfur dyes have a wash-fastness rated between 3-4, which is fair due to the relatively large size and partly to the aqueous insolubility of the dye molecule. The general lack of any significant polar groups in the dye molecule implies that the dye is retained in the amorphous regions of the fiber polymer system due to its size, aqueous insolubility and van der Waals forces of attraction.
Color Range of Sulfur Dyes
Sulfur dyes have a color range, which is limited to black, brown, blue and olive. Sulfur dyed textile materials are also dull. Their dullness can be attributed to the greater scattering of the incident white light, possibly due to aggregates of the dyed molecules trapped and entangled in the amorphous regions of the fiber polymer system.
Bronzing
Sulfur dyed textile materials show a metallic or bronze sheen, which is termed bronzing. This effect gives rise to poor rub-fastness, and moreover, gives the textile material a less appealing appearance. Bronzing mostly occurs in heavy or dark shades for the following reasons or combinations thereof:
(i) Exposure to excessive heavy dyeing.
(ii) Exposure of the textile materials to atmosphere during dyeing causing premature oxidation.
(iii) Failure to remove excess dye liquor following dyeing.
(iv) Providing an insufficient amount of sodium sulfide in the dye liquor to keep the dye in its soluble form.
The bronzing effect can be removed by an after-treatment in an aqueous solution of dilute sodium sulfide, which will remove excess dye molecules that are present on the surface of the textile material.
Cost of Sulfur Dyes
The relative low cost of sulfur dyes has meant their continued use particularly for dark colors, such as navy and black.
References:
[1] E.P.G. Gohl and L.D. Vilensky, Textile Science, Longman Cheshire, Melbourne (1989).
[2] A Fritz and J. Cant, Consumer Textiles, Oxford University Press, Melbourne (1986).